Over the last few decades, industries have been moving from manual operations to automation. That is because automation allows industries to operate faster and reduce the overall workload by integrating machines that handle such tasks. Automation allows industries to scale because machines can easily produce a lot more than manual labor.
One important asset in industrial automation is Programmable Logic Controllers (PLCs). PLCs, are industrial computers used to control how distinct electromechanical processes in manufacturing industries, plants, and other industrial environments operate.
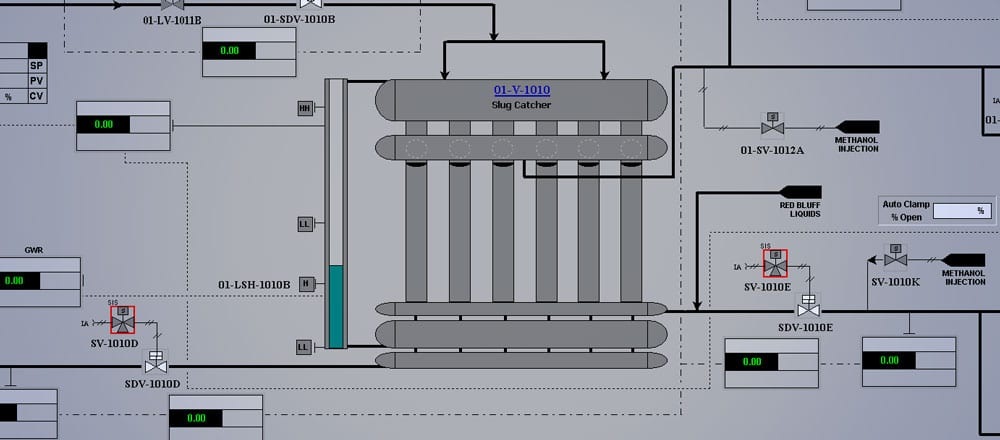
PLCs come in different forms and sizes, some small enough to fit in a palm, while others are magnificent enough to require heavy-duty racks. Others are easily customizable using functional modules and backplanes to fit easily in industrial machinery and applications.
How is PLC Designed and Programmed?
Industries prefer to use PLCs for automation because they are fast, easily programable, and ready to use. Besides, they can be easily customized to fit into industrial equipment, hence they don’t require a lot of space in plants and industries.
There are various ways of programming PLC to ensure proper functionality. Some are programmed using a ladder logic tactic, which uses electromagnetic relays to operate, while others are programmed using modified programming languages such as C and BASIC. Most industrial PLCs’ most common programming languages include Structured Text, Ladder Diagram, Function Block Diagram, Sequential Function Charts, or Instruction List.
How Do PLCs Work?
HMI and SCADA systems allow users to access and view data from the plant’s devices and manufacturing floors. They also have interfaces that serve as the control unit for manufacturing floor devices. PLC systems serve as physical interfaces between the manufacturing floor or plant’s devices and HMI or SCADA systems. They act as the communication, control, and monitoring devices for the automated processes of industrial machinery, assembly lines, and robots.
What are the Three Major Categories of PLCs?
PLCs are divided into three major categories depending on their uses. These three categories are CPUs, input, and output devices. Input PLCs are those control systems that monitor input data for the connected devices and machinery. The input data is then redirected to CPU PLCs, which process the data and apply logic. The processed data is then executed by the CPU PLC, which executes a user-designed logic, before redirecting that data to the output PLC which commands the connected devices and machines using the instructions in the output data.
A P L C System Integrator helps bring all these functions together; the input, CPU, and output. These integrators are designed using a combination of hardware and software that makes it easy for the three PLC categories to communicate and operate smoothly. They allow for the smooth flow of the automated process, ensuring that there are no delays in automated industrial operations. Besides, they have panels for human control, giving users a space for human-facilitated inputs. The human control panel can be a mechanical switch, button, encoder, or LCD screen that allows for human input.
Final Thoughts
A PLC is a Programmable Logic Controller that allows automation of industrial operations. It makes it easy to automatically control industrial machinery using input, processing, and output panels. The three detect industrial operations, process the detected data, and produce the desired output to control industrial machinery to produce the desired results effectively.